Non-Destructive Testing
Non-Destructive Testing (NDT) at Aeropol
We provide advanced in-house Non-Destructive Testing (NDT) services to ensure the integrity, reliability, and safety of critical components without compromising their usability. Our state-of-the-art techniques allow us to detect even the smallest defects and anomalies in materials, enabling predictive maintenance and quality assurance for aviation MRO.
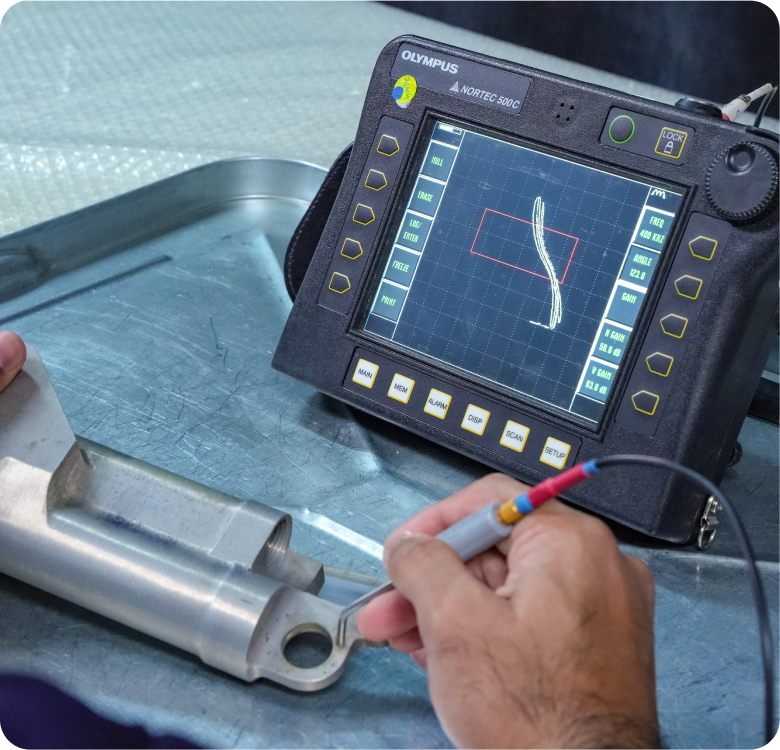
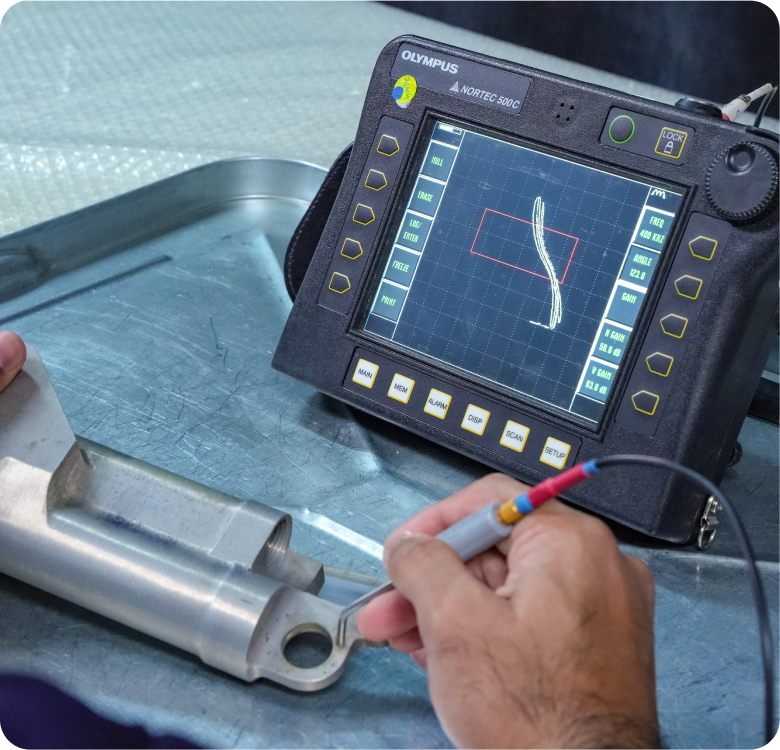
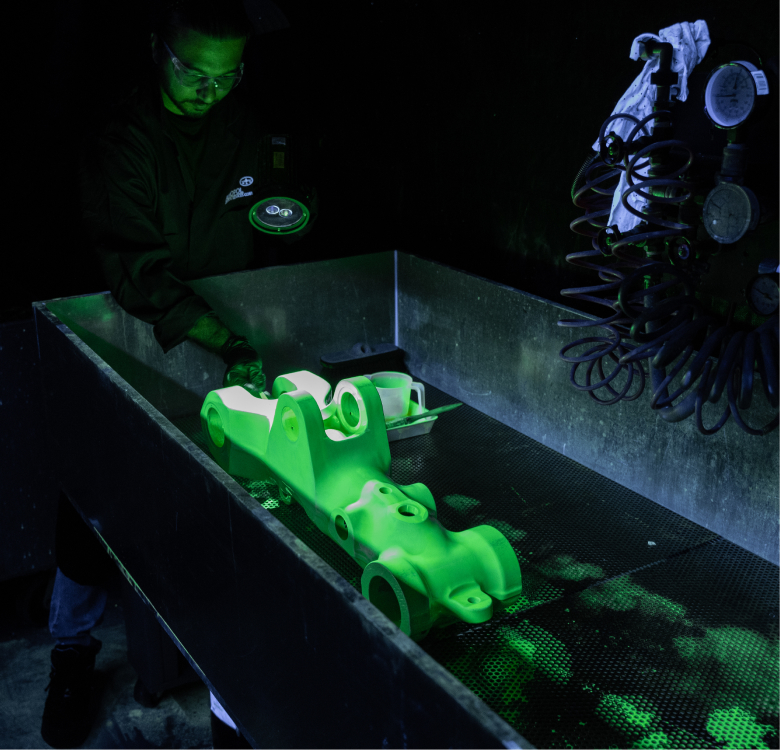
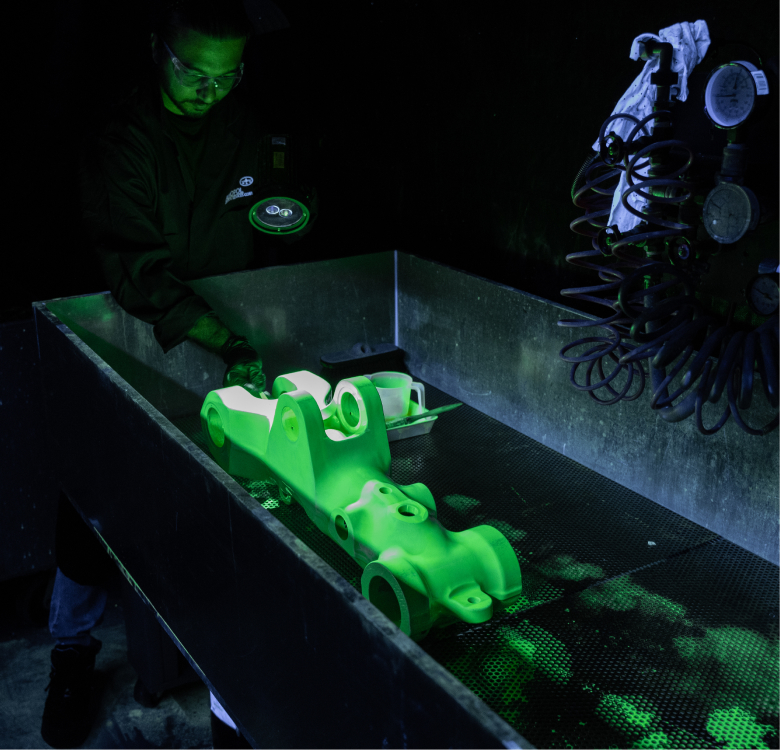
Eddy Current Testing
Eddy Current Testing (ECT) is one of our key NDT methods, ideal for inspecting conductive materials. By inducing electrical currents and analyzing the resulting electromagnetic response, we can identify surface and near-surface defects such as cracks, corrosion, and fatigue. This technique is widely used in aerospace due to its accuracy, speed, and non-invasive nature. Eddy current testing is highly effective on metallic components, ensuring minimal downtime while maintaining the highest safety standards.
Fluorescent Testing
Our fluorescent testing process involves applying a fluorescent penetrant to the surface of a component, followed by a developer that helps reveal surface-breaking defects under ultraviolet light. This method is particularly useful for detecting small cracks, leaks, and porosity in non-porous materials like metals, plastics, and ceramics. With its high sensitivity and ability to cover large surface areas, fluorescent testing is a valuable tool for ensuring precision and reliability on aircraft components.
Magnetic Particle Inspection (MPI)
Magnetic Particle Inspection is a crucial tool in the maintenance and inspection of aircraft components, it works by applying a magnetic field to a ferromagnetic material (like steel or iron), which induces magnetic lines of force to flow through the material. If there is a surface or near-surface defect, such as a crack or a void, it will disrupt the magnetic field, causing a leakage of magnetic flux. Magnetic particles, usually in the form of dry powder or liquid suspension, are then applied to the surface of the part. The particles accumulate around these leakage points, making the defects visible under proper lighting. with its quick results and effectiveness in identifying critical defects in ferromagnetic materials make it indispensable in the aviation industry.